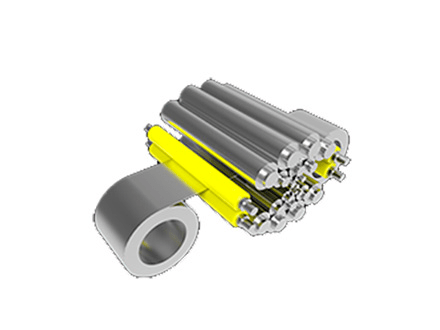
Because of its high rigidity, the 20-high rolling mill is currently the main type of stainless steel cold rolling in the world, while Sendzimir and Sundwick rolling mills account for about 90% of the 20-high rolling mill.
1 Roll System Configuration of 20-high Mill
The 20-high rolling mill is arranged in a reversible single stand, with flexible production and a large product range. The roll system diagram is shown in Figure 1. It adopts a tower-shaped roll system arrangement, and the rolling force is transmitted from the work roll to the support roll device through the intermediate roll, and finally to the upper and lower racks. The work roll is supported at multiple points along the entire length, and the bending deformation of the roll is extremely small, and a very accurate thickness deviation can be obtained in the width direction of the rolled piece.
The roll system of the rolling mill is divided into two groups, each with 10 rolls. Each group consists of one work roll, two one-middle rolls, three two-middle rolls and four support rolls. The support rollers use saddles and segmented bearings to achieve multi-point support, and the rest of the rollers are directly stacked without fixed support. Among the six upper and lower two intermediate rollers, 4 are driving rollers and 2 are driven rollers. The rollers are driven by friction.
2 The characteristics of the 20-high Sendzimir Mill
2.1 Rolling Mill Stand
The Sendzimir 20-high rolling mill is a closed-end rolling mill with an integrated stand, as shown in Figure 2. The frame is integrally cast with high rigidity. 8 plum blossom boring holes are processed in the integral steel casting to install the supporting roller device, which ensures that the rolling force is evenly distributed on the frame and reduces the uneven deformation of the roll system. The equipment is light in weight, only one-third of the four-high rolling mill of the same specification. The rolling mill has a small size and requires less capital investment.
Twenty rolls are inlaid in the frame according to the ring superposition. The rolling mill uses a heavy-duty side frame and a tapered top and bottom plate structure that tapers from the middle to the front and rear sides of the rolling mill, so that the deformation of the rolling mill housing under load is more evenly distributed along the width of the rolling mill, with “zero crown” Features.
The roll system of the rolling mill is divided into two groups, each with 10 rolls. Each group consists of one work roll, two one-middle rolls, three two-middle rolls and four support rolls. The support rollers use saddles and segmented bearings to achieve multi-point support, and the rest of the rollers are directly stacked without fixed support. Among the six upper and lower two intermediate rollers, 4 are driving rollers and 2 are driven rollers. The rollers are driven by friction.
2 The Characteristics of the 20-High Sendzimir Mill
2.1 Rolling Mill Stand
The Sendzimir 20-high rolling mill is a closed-end rolling mill with an integrated stand, as shown in Figure 2. The frame is integrally cast with high rigidity. 8 plum blossom boring holes are processed in the integral steel casting to install the supporting roller device, which ensures that the rolling force is evenly distributed on the frame and reduces the uneven deformation of the roll system. The equipment is light in weight, only one-third of the four-high rolling mill of the same specification. The rolling mill has a small size and requires less capital investment.
Twenty rolls are inlaid in the frame according to the ring superposition. The rolling mill uses a heavy-duty side frame and a tapered top and bottom plate structure that tapers from the middle to the front and rear sides of the rolling mill, so that the deformation of the rolling mill housing under load is more evenly distributed along the width of the rolling mill, with “zero crown” Features.
2.2 Press Down the System
The pressing is achieved by rotating the eccentric ring of the two upper middle support rollers B and C. The structure of the B and C rollers is shown in Figure 3. The rotation of the eccentric ring of the B and C rollers is to press down a pair of sector gears meshed with the double-sided rack by moving up and down, so as to rotate the eccentric shaft to realize the pressing and lifting of the work roll. The eccentric ring is installed on the needle bearing of the saddle, so it is much smaller than the movement resistance moment of the screw of the ordinary rolling mill. The 20-high rolling mill can also rotate very lightly and flexibly during the rolling process.