During the production of copper and copper alloy strips, there are various organic and inorganic contaminants on the surface after the strip is annealed and rolled. If it is improperly handled or in a high-heat atmosphere, the surface of the copper strip will be oxidized, and the remaining rolling oil will also contaminate the surface of the strip. If the intermediate products are improperly stored, they can also cause surface discoloration. With the wide application of copper strip products in modern industry, the requirements for its surface quality are getting higher and higher. In order to obtain high-quality copper strip, it is very important to strengthen its surface cleaning. As a result, copper strip surface cleaning technology and equipment are generally valued.
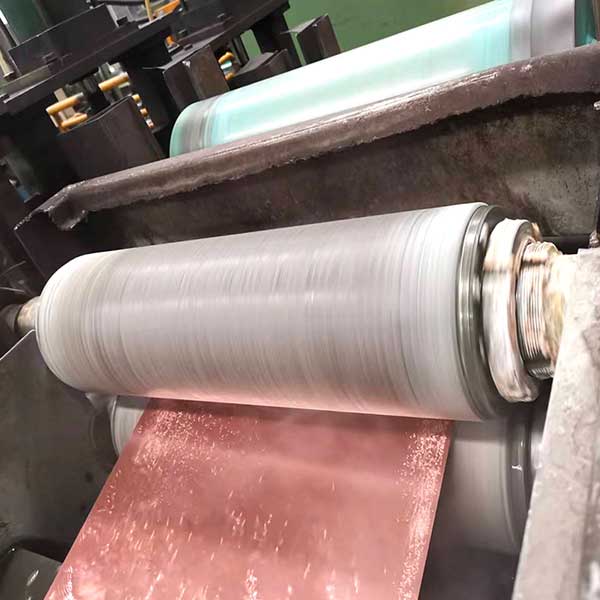
1 Copper Strip Surface Cleaning Technology
1.1 Degreasing
The purpose of degreasing is to remove organic contaminants on the surface of the copper strip, especially the remaining rolling oil and the mechanical oil mixed into it. Degreasing is mainly set up for treatment before pickling and surface polishing. If the degreasing is not complete, the oxides on the surface of the copper strip cannot be completely cleaned by acid. Degreasing methods include: solvent degreasing, lye degreasing, electrolytic degreasing and ultrasonic degreasing.
1.1.1 Solvent Degreasing
Degreasing solvents include petroleum-based, chlorine-containing, fluorine-containing and surfactants. Petroleum systems are easy to cause fires, chlorine systems are carcinogenic, and fluorine systems are damaging to the ozone layer, so they are rarely used. Recently, more surfactants have been developed. Surfactants bring lipophilic bases into molecules and emulsify oil in water to achieve degreasing.
1.1.2 Lye Degreasing
Animal and vegetable fats and oils are decomposed with alkali and hydrolyzed to produce high-grade sodium fatty acid (soap) and glycerin. This saponification reaction achieves degreasing, and the resulting soap acts as anionic surfactant to help degreasing. but. Rolling oil is mineral oil, mainly petroleum aliphatic carbohydrates, and does not undergo saponification. Therefore, surfactants should be added in alkaline degreasing.
1.1.3 Electrolytic Degreasing
Electrolytic degreasing is a very effective method. It is usually energized in an alkaline degreasing solution. The water is electrolyzed. Cathodic electrolysis (copper tape is used as the cathode) produces hydrogen, and anode electrolysis produces oxygen. The bubbles produced can peel off surface contaminants. . The hydrogen produced by cathodic electrolysis is twice that of oxygen, and the reduction effect of hydrogen also activates the surface. Therefore, the electrolytic degreasing of copper strips adopts the cathodic electrolysis method, but attention should be paid to the precipitation of metal impurities in the degreasing solution and the occurrence of excessive degreasing. The addition of cyanide helps prevent the precipitation of metal impurities, but it has pollution problems and must be used strictly. Anode electrolysis, due to the oxidation of oxygen, can remove the preservative on the surface of the copper strip that cannot be removed by cathode electrolysis, but it is prone to excessive degreasing.
I. 1.4 Ultrasonic Degreasing
Ultrasonic Degreasing Cleaning Machine is composed of an ultrasonic signal generator and a degreasing cleaning tank. The ultrasonic signal generator generates a high-frequency oscillation signal (sine wave), which generates tens of thousands of high-frequency mechanical oscillations per second through the transducer, and forms ultrasonic waves in the degreasing fluid, which alternates between positive and negative pressures at high frequencies. The forward radiation propagation (with direct radiation, reflection and refraction functions) in the dense and dense intermittently causes the degreasing fluid to continuously produce countless tiny bubbles and continue to burst. This phenomenon is called the “cavitation effect”. When the bubble bursts, an instantaneous high pressure above 1,000 atmospheres is formed, producing a series of explosions, releasing huge energy, and forming a huge impact on the surface of the copper strip, causing the oil to quickly peel off the surface of the strip, achieving the purpose of degreasing and cleaning. Using ultrasonic solvent degreasing, if the surface of the copper strip is slightly oxidized, pickling is not required. The passivation agent is added to the cleaning agent to complete the passivation while cleaning, which greatly simplifies the degreasing cleaning process and equipment.
1.2 Pickling
Compared with mechanical surface cleaning, there are two types of chemical cleaning of copper strip surface: pickling and dipping. The method of removing the thick oxide film on the surface and immersing the copper strip in the acid solution for a long time is called pickling; and the method of removing the oxide film and immersing the copper strip in the acid solution for a short time is called dipping. Traditionally, these two methods are collectively referred to as pickling. Copper strip pickling solution usually uses sulfuric acid solution, and the concentration depends on the degree of oxidation of the copper strip surface. The surface oxidation of modern copper strip production is relatively light, and most of its pickling uses a sulfuric acid solution with a concentration of 5% to 15%. The temperature is room temperature, and some are heated to 60°C. The time of using through-type pickling ranges from 10 to 60 seconds. The specific pickling process parameters should be adjusted according to different copper strip varieties and surface conditions. The concentration of brass acid solution is relatively low, and bronze and red copper are relatively high. In order to strengthen the effect of copper-nickel alloy pickling, oxidants such as nitric acid and hydrogen peroxide are mixed into the sulfuric acid solution. However, because nitric acid has NO: volatilization, it should not be overused. Hydrochloric acid will generate chloride-based corrosive media, which will accelerate the discoloration of copper strips and corrode equipment, so it should be avoided. Generally speaking, the combination of pickling and grinding can achieve good results.
1.3 Grinding and Cleaning
Grinding methods include polishing, roller brushing and roller grinding, etc., to clean the mechanical surface. Add abrasives such as silicon carbide, alumina, etc. to the polishing wheel made of cloth, linen, resin, etc., or use a nylon (polyamide) wire brush coated with alumina. Mechanical brushing to clean the surface of the copper strip. In order to improve the quality of copper strip surface polishing and grinding, degreasing cleaning, pickling, polishing and grinding are usually combined into a production line. When polishing and grinding, for different types of copper belts, belt thicknesses and surface conditions, different polishing and grinding brush rollers and nylon (polyamide) filament wire diameters, particle sizes, or brush roller meshes and hardness should be selected. For polishing wire brushes coated with alumina, a polishing brush with a wire diameter of 0.25-0.3 mm and a particle size of 500-600 mesh is usually used. For the abrasive brush roller made of non-woven fabric, the particle size is 1500~2000 mesh, the hardness is 40 (soft) or 60 (medium). For products with higher requirements on the surface of copper strips, abrasive brush rollers with a particle size of 250,000.3,000 meshes can even be used. The higher the mesh, the shorter the service life of the brush. When in use, adjust the contact pressure between the polishing brush and the surface of the copper strip, or the amount of grinding of the grinding brush roller, and the appropriate brush roller rotation speed according to the surface condition of the copper strip. For rough-rolled and annealed tin-phosphorus bronze strips, in order to remove surface defects caused by casting and rolling and improve the surface quality of the strips, elastic grinding wheels with a lower mesh number (220 mesh) are often used. A simple surface polishing is performed on the thick strip. Wanfang Data No. 2 Gong Shoupeng: Copper Strip Surface Cleaning Technology and Equipment 71 Although this treatment increases the metal loss on the surface of the strip, it will play a significant role in improving the surface quality of the copper strip. This method is also effective for removing and improving the surface of the brass strip produced by horizontal continuous casting due to improper melting and casting process and operation.
1.4 Surface Passivation (Rust Prevention) Treatment
Because the copper metal itself is Lewis alkaline, it is easy to lose electrons and oxidize, especially the copper alloy itself has a negative potential difference, which is very easy to be oxidized in a humid and hot environment and cause discoloration. Therefore, the prevention of discoloration after cleaning is also an important part of the surface treatment of copper strips. Traditional anti-tarnish treatments include chromate passivation and benzotriazole (BTA) passivation. Chromate has strong oxidizing properties and can form an inactive passivation layer on the surface of copper, thereby playing a protective role and having a good passivation effect. Due to environmental constraints, this purification method can no longer be used on a large scale. Benzotriazole and its derivatives have a good effect on inhibiting the corrosion of copper, and it is currently the most widely used passivator. The passivation mechanism of BTA (C. H5N,) is that the H in the NH group of the BTA benzene ring is repeatedly coordinated and combined with monovalent copper to form a polymer-like compound film, which has a strong bond with the strip. force. According to the data, the film thickness can reach 5×10~ttm, and the thermal stability is 300. C, the melting point is lower than 100. C, stable performance in pH3-12. When used, the concentration of the aqueous solution is 0.5%-1% (weight percentage), and the temperature is 60-80°C. Due to the limited solubility of BTA in water, it is best to dissolve it with a certain amount of alcohol when preparing it, and then pour it into soft water. In recent years, a new type of copper alloy passivation agent CC-2002 has been developed in China. It is based on BTA with a variety of organic additives. The liquid preparation, use and maintenance are very simple. The anti-tarnish effect is significantly improved compared with traditional BTA, and it does not contain heavy metal ions and environmentally harmful chemicals, and the pH is close to neutral. , No corrosion to equipment, no irritation to skin, is a new type of passivating agent worthy of popularization and application.
2 Copper Strip Surface Cleaning Equipment
The copper strip cleaning unit is a special equipment developed in the past 20 years, and it has been continuously improved and perfected in actual use. Usually, the copper strip cleaning unit is composed of different functional units. These functional units include degreasing and washing units, pickling and washing units, polishing and washing units, and passivation and drying units. Different functional units can form copper strip surface treatment production lines for different purposes, such as: surface degreasing production line; surface degreasing and pickling production line; surface degreasing, pickling, polishing, grinding, and passivation production line. In addition, due to the long cleaning line of the multifunctional unit combination, the large floor space and the inconvenient operation at the front desk, the cleaning line layout has recently developed a double-layer copper strip cleaning line in addition to a single layer. The single-layer layout of the copper strip cleaning production line is shown in Figure 1, and the double-layer layout of the copper strip cleaning production line is shown in Figure 2.
2.1 Copper Tape Stitching
The stitching of the head and tail of the two rolls of copper tape generally uses a hydraulic strip stitching machine, equipped with two upper and lower dies, a hydraulic system, and front and rear guide plates. Use upper and lower concave-convex dies to punch the joints and insert copper wires to connect the two strips. Whenever the stitched part of the strip passes through the pinch roller, squeeze roller or brush roller, these rollers will automatically lift to prevent damage. After the stitched part has passed, the roller will automatically be pressed down. Recently, the argon arc spot welding method of stitching strips has begun to be used in cleaning machines due to its simple operation.
2.2 Degreasing and Washing Unit
The unit usually consists of a strip degreasing chamber, a cold water cleaning chamber, several pairs of encapsulated squeezing rollers, a degreasing agent storage tank, a circulation system and a heating device. In recent years, in order to enhance the degreasing effect, spray pre-degreasing has been added in front of the degreasing room. The degreasing chamber is equipped with a nylon (Belon) wire brush roller without abrasives and a reverse pressure roller. The brush roller motor current can be adjusted to adjust the pressure of the brush and the strip. Hyundai’s degreasing unit is also equipped with degreasing agent filtration and automatic oil-water separation devices. The oil-water separation of the degreasing agent is not good, which will cause the degreasing effect to decrease.
2.3 Pickling and Water Washing
The strip pickling tank structure has two types: simple single-layer through type and upper and lower two-layer type. Modern copper strip pickling adopts a lifting type upper and lower two-layer circulating pickling tank structure. The lower layer stores acid, and the strip passes through the upper layer. If the strip needs to be pickled, start the acid circulation pump to lift the lower layer of acid to the upper layer, so that the strip is completely immersed in the acid. Since the acid liquid immersed in the strip is in a flowing state, the pickling effect is better. If the strip does not need pickling, just turn off the acid pump, the upper layer of acid will flow back to the lower layer, and the strip will pass directly. There is acid liquid on the surface of the copper strip after pickling. Usually, two pairs of squeezing rollers are arranged at the outlet of the acid tank, and after squeezing, they enter the cold water washing chamber composed of pipes and nozzles.
2.4 Polishing, Drinding and Scrubbing
Polishing, grinding and brushing are very important links in the surface cleaning of copper strips. It is usually carried out in a scrubbing box equipped with a polishing brush or abrasive brush and rotating at a high speed, while spraying a large amount of water to rinse. There are many types of brush rollers, ordinary nylon wire roller brushes can be used for general brushing; for polishing and grinding the belt surface, the spirally arranged roller brushes with aluminum oxide or silicon carbide (Anderlon) or high-strength artificial non-woven fabrics are often used. Abrasive grinding roller made of fiber. For copper belts with a bandwidth of 4001Tlnl or less, the polishing and grinding brush rollers can adopt a cantilever structure. For the belts with a bandwidth greater than 400ram, most of the structures are supported at both ends of the brush roller. Equipment manufacturing accuracy, brush roller dynamic balance and installation conditions will affect the surface polishing and grinding quality of the strip, and even leave the strip unusable due to obvious brush marks. The rotation speed of the brush roller can be as high as 750-l200 rpm. It is also possible to increase the number of abrasive brush rollers and arrange different types or meshes of abrasive brush rollers before and after to clean the surface of the copper belt to improve the surface cleanliness.
2.5 Multi-level Utilization of Flushing Water
A copper strip cleaning production line with degreasing, pickling, polishing, grinding and passivation functions, each functional unit needs to be equipped with cold water washing. If the flushing water of each unit is supplied and discharged separately, the water consumption is very large. Therefore, a multi-stage water flushing device called “reverse supply” was introduced. It divides the flushing water tank into several separate water tanks. The polished flushing water returns to the No. 1 water tank. The water from the No. 1 water tank is used as the rinsing water after the strip pickling. The rinsing water returns to the No. 2 water tank. Used for rinsing after strip degreasing and draining back water. Since the polishing water is accompanied by more copper powder and other particles, a separate belt filter must be equipped, and it can be recycled after being filtered.
2.6 Passivation and Drying
Recycled passivating agent can be sprayed or immersed to react with the passing copper tape to form a passivation film on the surface to achieve the effect of rust prevention. The temperature of the hot air in the drying room is about 80°C, and usually a hot air circulation fan and a dehumidifying fan are used for heating. In order to ensure that the surface of the copper strip is dried after passing through the drying chamber, the surface moisture of the copper strip entering the drying chamber must be removed first. For this reason, two pairs of rubber squeezing rollers are often equipped with “air knives” to blow away residual moisture. Recently, 3M millennium rollers (Mill Roll) have been used instead of rubber squeezing rollers. Millennium roller is a kind of high-strength porous non-woven fiber disc structure roller with better squeezing effect. Special attention should be paid to the use of millennium rollers to avoid excessively sharp corners and cracked edges of the copper tape to cause damage to it.
3 Conclusion
The copper strip cleaning equipment composed of different functional units can not only meet the requirements of the surface cleaning of the finished copper strip, but also can be used for the surface cleaning of the copper strip in the intermediate process, and even be used for the grinding and removal of the surface defects of the rough rolling blank. With the continuous improvement of customers’ requirements for the surface quality of copper strips, the development of copper strip surface treatment technology and equipment has increasingly attracted the attention of copper production plants and equipment manufacturers, and has become an important part of copper strip production technology and equipment, which has increasingly shown Its importance.